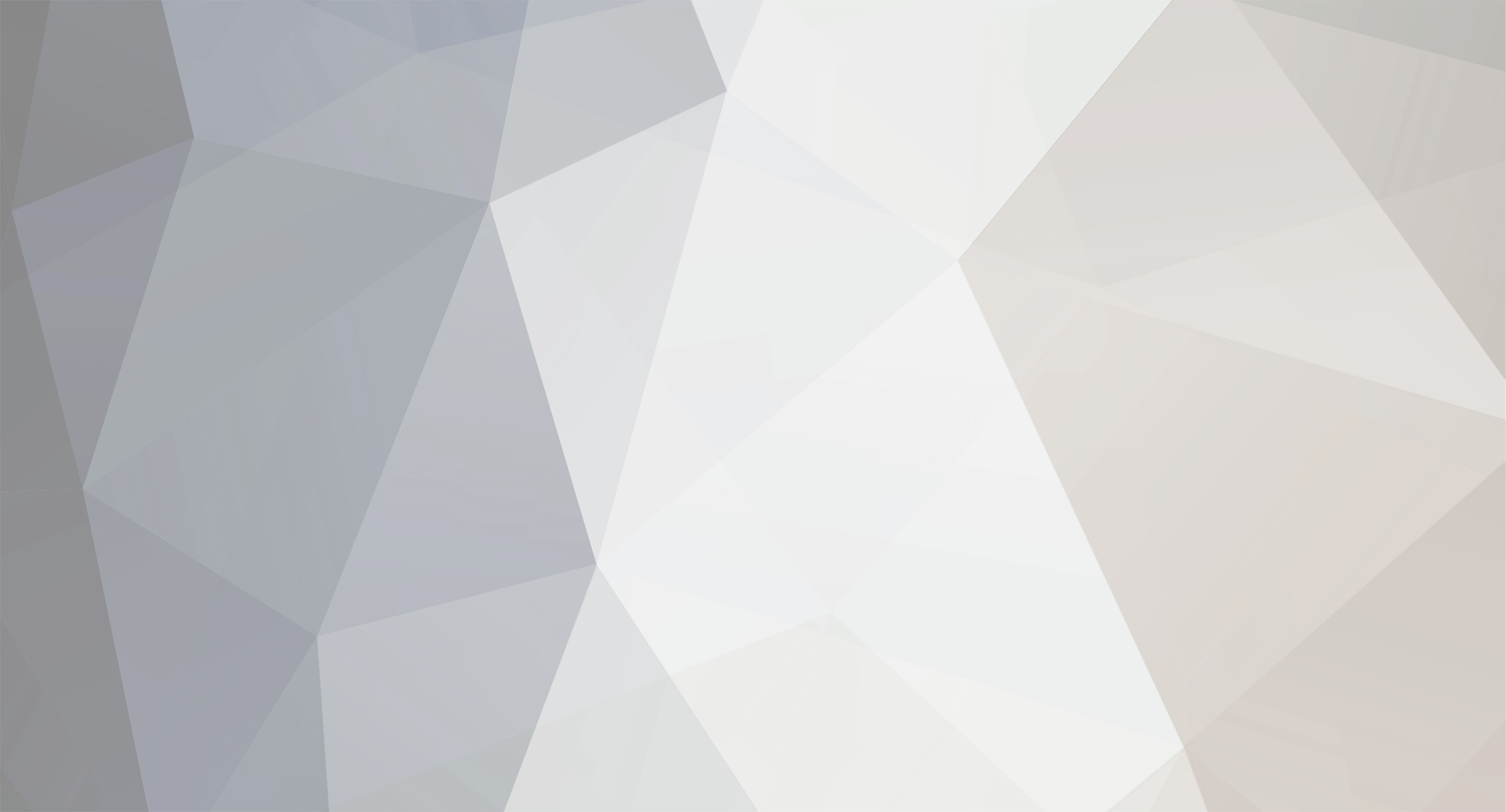
Larason2
Gold Tier-
Posts
245 -
Joined
-
Last visited
Content Type
Profiles
Forums
Events
Store
Downloads
Gallery
Everything posted by Larason2
-
The fifth year of Showa was actually 1931. The forging on this blade is very basic, and the pattern is acid etched. The characters on the blade look applied on, maybe with solder? and some of the strokes have fallen off. There doesn't seem to be any evidence the blade is differentially hardened, no hamon or even a difference in the metal (Japanese swords are traditionally laminated). The nakago (tang) is not filed, as it would be traditionally, and the edges on it are not straight, and it is not straight. The characters on the nakago are crudely carved, and don't follow proper stroke order and direction. There are large forging defects in the nakago as well. I can't see much of the habaki, but it looks like it is of uneven thickness, poor quality metal, and poorly worked. So overall, likely a Chinese reproduction.
-
AFAIK, nioiguchi is the hamon line, but more importantly, is the presence of nioi or nie in the blade in that area. It's possible there's Japanese smiths working in China or some other place who make these "Komonjo specials," however, we don't know, and are unlikely to ever know where they come from. I would definitely say though that there are native Chinese smiths that have the skills to make such a blade. To get the fine hada seen, the steel has to be folded 10 times, and the steel used here is probably some kind of orishigane. I doubt you can get good nioi or nie with anything other than tamahagane though. As for the polish, it's not surprising they cut corners! I strongly suspect all these are oil quenched, which is the standard for all blades in China.
-
I have more than a few blades like this, also purchased from komonjo. I wouldn't have bid on this one though, because I consider the start of the hamon to have been hardened too far from the edge in several spots. It's not a problem for display, but may be a problem if you plan to use it! It's hard to see, but I suspect yours has been machine ground on the end of the nakago, and the flash was not filed off, a tell tale this is Chinese. Also, as mentioned, no nioi or nie to speak of. Still, these "Komonjo specials" show a very fine hada, and are otherwise very well forged. The polishing isn't bad, but they are deficient in the time spent on the uchigomori and jizuya/hazuya steps (the most time consuming). Personally, I would be happy I found such a fine reproduction at such a low price! This is not a nihonto, however, but a good quality clone. Many other owners of these swords on another forum are very happy with these blades as reproductions. Try making one of these for the price you paid! There are a lot of different words for "new" Japanese swords, and they mean different things to different people. Gendaito, shinshinto, and shinsakuto are just some of them. You also hear Showa a lot, but less so Heisei or Reiwa. There's more than one forum post on the NMB about this, and there seem to be different opinions about what they mean, and no agreement! I think the best is just to say when it was made if you know, and use "recently forged" in English instead of the Japanese names, since they can be confusing.
-
Dale, I'd say the advanced deterioration has actually improved that one! 5000 yen is still a bit much though! Now we know how to make a cast tsuba nicer; bury it in the ground for a while!
-
Thanks for sharing the picture. You can see all the different colours of metal they used to cast it. Whatever metal they had at hand, and would fit in the electric arc furnace! The interior of the cast tsuba I have looks identical.
-
Corrections accepted gentlemen! Yes, it is more complicated than it at first seems, and I have to keep reminding myself. So far, my only experience with iron/steel forging has been hot, and in my limited experience wrought iron has been a bit harder to work with, because it needs more heat. That's a good reminder though that wrought cold forges nicely! It's not always practical to fire up the forge, so I really should spend some time cold forging the wrought pieces I have that are close to ready. I also like Jean's definition, and I will endeavour to use it in the future.
-
Luc, the only difference between "wrought iron" and "steel" is that the iron has layers of silaceous impurities between the layers of steel. A blank of the same thickness of either material, assuming it hasn't been hardened, will be exactly as difficult to hammer as the other. This isn't subjective, it's a reality of the material. If you find any steel to be hard to hammer, all you have to do is anneal it; heat it up to red heat with a propane torch, and let it slowly cool in the air, and you will find it easy to hammer.
-
Agreed. You can get tamahagane, but it's very expensive. For armour, mild steel is a reasonable alternative. You're just going to lacquer it with urushi anyway!
-
I think you removed the patina. You have to be very careful with rokusho/niage, the patina is sometimes a single molecule thick! The surface needs to be restored with a tsushima do stone or something similar, then magnolia charcoal, and repatinated with rokusho. The face of the figure is indeed shibuichi. It tends to darken with time. A fringe benefit of needing to repatinate it is you can use the magnolia charcoal to restore the original colour of the figure's face, which would have been much lighter.
-
That's true! You can't really make a kinko tsuba magnetic.
-
Magnetism is complicated. Steel, cast iron and wrought iron can all be magnetic, but they can all also be demagnetized. One way to demagnetize a magnet is to strike it repeatedly with a hammer. One way to magnetize something is to strike another ferromagnetic metal with it. So both forging and chasing, which are used to shape tsubas, may affect the magnetism of a ferromagnetic object like an iron tsuba. So I agree the magnet test isn't very useful. Better to use other means of establishing what something is made of.
-
Wow, it did turn out very nice. That's a very understated hamon!
-
Great article, thanks!
-
I agree cast copy, though I quite like the design it was based on. You can see casting bubbles in the keshikomi zogan (the "dots"), and they forgot to paint one or two of them! The colour isn't right for gold. The "characters" aren't well formed, definitely not engraved, and hard to read because of stray marks, and yes, the seppa dai (part in the middle the seppa sit on) is distorted. Also, the design is identical front and back! You'd never see that on an authentic Japanese tsuba, they always varied the design on the reverse (ura). Not sure we'd be able to get a translation of the mei with the characters being so hard to make out. Thanks for sharing anyway!
-
I agree all swords need some kind of a hand guard for protection, even if their principal use is for movements with low risk to the hands. The first bronze age swords didn't have provision to protect the hand, but the first modifications done to this basic design was to add a ridge at the bottom of the blade on each side to protect the hand. There's hardly any swords that didn't have a hand guard from any culture after this, so I suspect that it has been considered an essential aspect of a sword everywhere! The hand is one of the most vulnerable parts of the body to a sword, makes sense to protect it.
-
Haha, on that flower I see a dimple on some of the leaves! Nature is complicated!
-
Looking more closely at the plum blossoms online, the ones I thought were divided were actually more than one petal. So I will accept the correction! As they say, I've never learned anything from an argument I've won!
-
There's lots of pictures of the plum online with an indentation in their leaf. If cherry blossoms are irregular, they tend to have a point on each petal, whereas if plum blossoms are irregular, they tend to have an indentation. Given that, in my opinion, an indentation is more representative of the plum. The plum blossom seems to be more common on tsuba, and when it's there, it usually has an indentation in the petals. That's my opinion!
-
I don't think plum or chrysanthemum. Usually plum has two lobes on each petal, and Chrysanthemum has way more leaves. My vote is cherry blossom, usually depicted with a more round leaf. The bar could be the cherry branch.
-
Interesting Arnaud, thanks. I didn't know about this process, I would be afraid it would become delaminated! My way of approaching this would be differential casting, but that has its pros and cons too. The hard part is casting a good copper without defects, and without a lot of copper oxide inside the tsuba to make it brittle. Differential casting is probably also more work!
-
Sorry to continue hijacking this thread, but I agree the weasel makes sense. There are weasels like the Japanese weasel "Mustela itatsi" that have a bushy tail. Personally I'm grateful to David for posting his tsuba, and I think it is a nice one. Overall, I think this thread is very appropriate for the tanuki; shapeshifter, jokester; with multiple cases of (possible?) mistaken identities and doubt in the minds of observers what was actually seen and what they are actually seeing, different opinions about what the Tanuki is, and whether or not something is actually a Tanuki! It's like we're crafting our own Tanuki legend right here on this forum!
-
Are you sure it's a mujina? Looks like a squirrel to me! Though I'm not sure there's any mammal with a neck that long!
-
Ford puts Borax and Alum into the solution. Helps to stabilize the elements that patinate, but it is optional. Some also put salt in as well, but Ford doesn't.
-
Darrel: I think you're right about the Shakudo. The 37.6% is actually from a 9 ct alloyed gold ingot. In my ignorance, I thought that was Shakudo! Here's the video it comes from: Thanks for the clarification!
-
Steve: On the first two photos, you can see a construction line, which is the change in patina close to the top of the ana. The shakudo layer is quite thin, something like 1mm. Vitaly: That looks like the right stone. "对馬黒名倉: tsushima black nagura" The tsushima do are coated on 5 sides with urushi to prevent them from disintegrating, which makes them look a little too slick, but the picture here shows the stone face on the top.