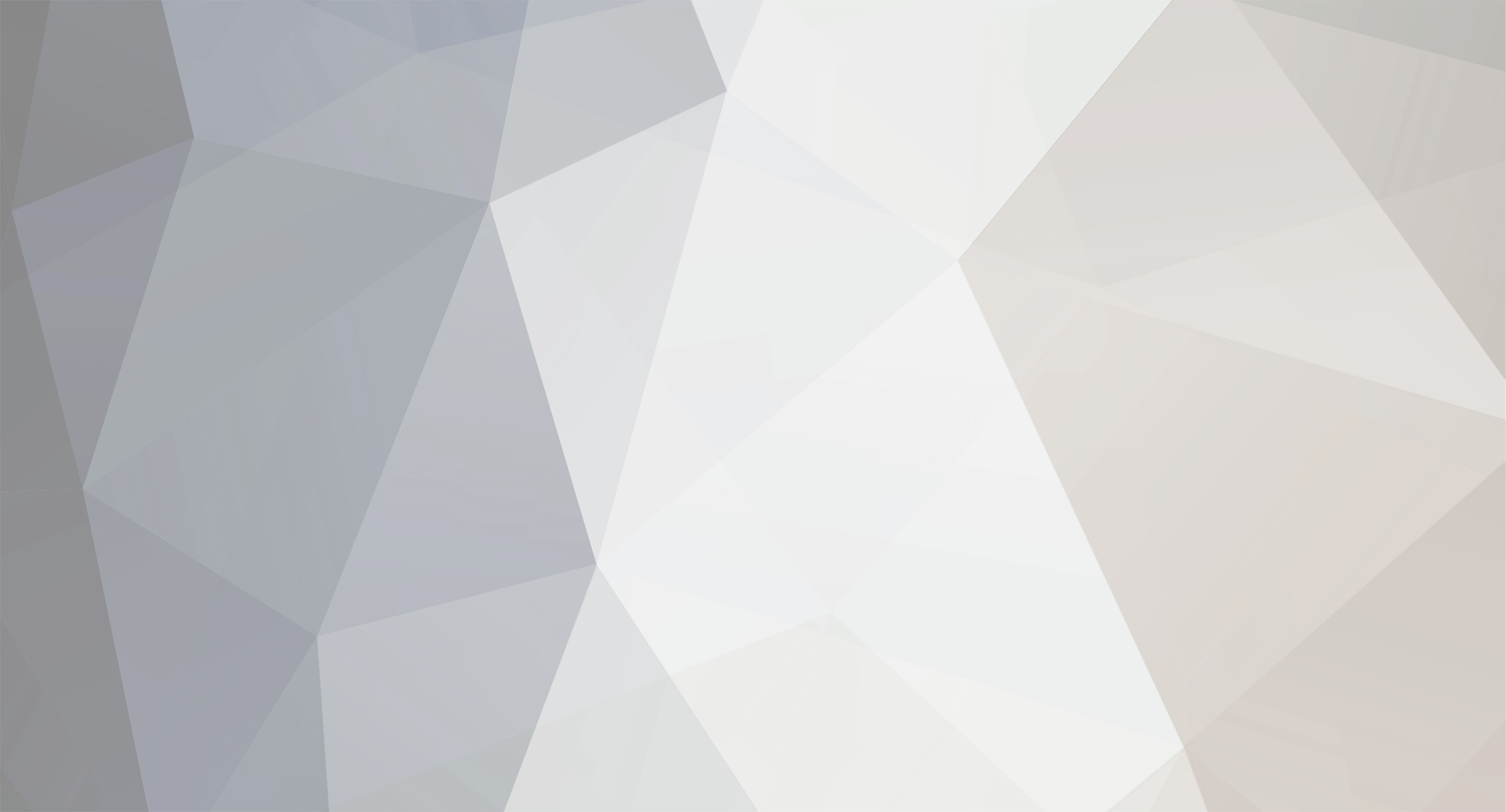
Larason2
Gold Tier-
Posts
245 -
Joined
-
Last visited
Content Type
Profiles
Forums
Events
Store
Downloads
Gallery
Everything posted by Larason2
-
Collectibles in general are falling off
Larason2 replied to drbvac's topic in General Nihonto Related Discussion
It's been a while since TokashikiBob asked the question, but I thought I would say something about it since I meant to before, but didn't get to. I don't think there is or will be a lot of collectors in China. Part of this is that the Chinese don't really consider Japanese blades to be superior to their own. In China they have a long standing history of sword manufacture, and many different periods, and I'm sure to them what kind of steel it's made out of or whether it's folded or not doesn't matter that much. If a wealthy Chinese person wants a fancy sword, they get a well made reproduction, possibly made out of meteorite metal. Those are expensive enough to give nihonto a run for their money! Also, the Chinese have a long history of the decorative arts that rivals the Japanese, so the Japanese decorations probably seem a lot like theirs. The next element of this is that control over import and ownership of swords is very tight in China, and it's probably not worth the headache to try and buy a Nihonto when you can just get a Chinese sword. -
I think it's a good price for a gorgeous blade. I'll take it if you don't want it!
-
help authentic long sword
Larason2 replied to samusamu's topic in General Nihonto Related Discussion
I agree this looks like a bokken (wooden practice sword). It would be nice to have more close up photos of each end and the area around the tsuba/hand guard. -
I am honestly interested and committed to learning about archaeo-metallurgy!
-
Jean is absolutely right. If you're interested, there's a Canadian who studied knife blade smithing in Japan, then returned to set up his own forge in Canada. He has videos showing how he made many of his own tools (similar process to his knives!).
-
Collectibles in general are falling off
Larason2 replied to drbvac's topic in General Nihonto Related Discussion
John and Baba, I think it will be very difficult for reproductions to ever get good enough that experts won't be able to tell the difference. The key thing there is polish. There are actually Chinese smiths who can make laminated and differentially hardened swords, along with koshirae suppliers in China that can custom make every part of a katana including the saya. If they were polished by a real togisho, then they would be really difficult to tell apart from a real Nihonto. However, a real togisho would never polish them, that's why they're so strict on authenticity, and there's no one in China that is willing to put in the work a togisho does. Also, those kind of swords start at something like $4000 USD, so at that point, you might as well be buying a nihonto. $2000 is actually a pretty reasonable amount per hour to polish a sword to the detail a togisho polishes it to, and each togisho actually has a treasure trove of expensive stones and other equipment that is very difficult to replicate anywhere outside of Japan. Baba is also right that there is a substantial market for low cost clones, and a fair number of people who think they're getting "the real thing." The day they try to cut with it and it snaps in half, or the when they show it to someone knowledgeable who tells them they have a "mall sword," or the day they try and sell it and find it's worthless, the illusion is dispelled. -
Collectibles in general are falling off
Larason2 replied to drbvac's topic in General Nihonto Related Discussion
I agree that the younger generations have less money to spend on collectibles, but also that their tastes are different than the older generations that buy a lot of these collectibles. I think that if that isn't shaking up the market now, it will eventually. However, I spend a fair bit of time also on the Sword Buyer's Guide forum, and what I see there is that there is strong interest among those who buy reproductions in nihonto and tosogu, just that most of them cannot afford them! So that may shake up the market at some point (if not now), but I think that for the younger generation they will at least be valued, and not thrown on the scrap pile! There are also a fair bit of collectors of reproductions who also have a few nihonto, so identity in the two groups isn't necessarily exclusive. I think a big driver of the sale of reproductions is that learning the art of the Japanese sword is popular, however no one wants to cut with their nihontos! Given the choice, I think most members of the younger generation would prefer a real nihonto to a reproduction for display or collection any day. -
Thanks Jean, I think your last post clarifies and settles the question for me. Modern Japanese sword making is really an extension of the bloomery process, so they never really got into casting for it. As mentioned, casted swords are no good, so the Japanese would never have bothered with it, even though they had a process for cast iron. So there's no question that the sword in the article was made using some sort of bloomery style process.
-
Thanks Jean, Dan and Jeremy. Jean, that was a helpful response, I think I'm starting to get what was going on. I think the problem is that many people (myself included!) refer to any high carbon iron as "cast iron." While it's true that cast iron needs a bit of a higher carbon content, not all high carbon iron can be cast, so it's probably better to only call iron that has enough carbon for casting and is/was cast as "cast iron." If high carbon iron is worked enough though, the iron particles in it increase in length, and it becomes "wrought iron" Now, the swords dug up from the early iron age are known to not be as good as the carbon steel swords we have now, and I suspect this is for a few reasons. One is that they weren't heat treated, an important reason why modern swords are so much tougher. Another though, is that they probably contained impurities including some grains of iron with a carbon content above 2.1%, which were a by product of the bloomery process by which many of them were made. Here's an interesting article that supports that: https://www.tf.uni-kiel.de/matwis/amat/iss/kap_a/advanced/ta_2_3.html So my thinking is that the "cast" iron sword in the original article is most likely one of these swords made from a bloomery type process. I would think that since by that time there was a fair bit of contact between europe/the middle east and asia, this basic process would have probably made it over there, or they independently discovered the bloomery process in asia, since it is in some ways similar to the bronze smelting that they obviously had experience with. So I think that is the default, and most likely technology used to make the blade referred to. I read on another page that Chinese iron casting started around 300 BC, so it could potentially be a technology used to make the blade. However, I don't think that's likely, because it wouldn't make a very good sword! There are some posters that suggested it could be ceremonial, like those Korean stone swords, but you usually don't have any ceremonial item that is known to otherwise be a dud. In fact, they would have to be careful not to drop it on something hard. Those Korean stone swords would break if used, but you could still use them to impale! Now, could they cast them, then work them to make them better? This is possible, but at that point, they're basically making wrought iron swords, which are a lot of work to make, and the result would probably still be inferior to the bloomery swords mentioned above. That's why wrought iron is so expensive even today! So this is possible, but I think also unlikely. I don't have access to the original article, but the way that the abstract is worded suggests to me that they are ignorant of the finer details of a bloomery iron vs. cast iron vs. wrought iron sword. It probably just has a bit higher carbon content, so they called it cast iron. So I think it is most likely bloomery iron. As stated on previous posts, the structure of the iron can vary a lot, since these swords were made so many different ways across the world.
-
Thanks all! Haha, I am actually a wannabe amateur sword polisher, but I think it's a crime to damage a real nihonto this way, so I'll confine my experiments to reproductions! There's really no way to polish a nihonto the way they do it without the training they have, and without the time they take to do it. The truth is also that there aren't really any youtube videos that provide any kind of useful information on the process. I've looked! Even if there was, there's no way you would be able to do it without the skills they have acquired. The problem is that I admire nihontos without the budget to buy one, and I'm a bit of a tinkerer, so I want my reproductions to look more like one!
-
Isao Machii split a stone
Larason2 replied to DoTanuki yokai's topic in General Nihonto Related Discussion
It's true, I want to see the sword after! I hope he did it with a reproduction, and not a nihonto. -
Thanks Jean. In some ways you are right, but in some ways there is more to it than that. Take a look at these three videos: It's true that in each one, the clay is different, and the design of the furnace is different, but in every other aspect, it's pretty similar. The bellows used are the same, the charcoal used is the same, and the basic principle is the same. Now, refractory clay and non-refractory clay are both just clay. Refractory clays just happen to have components that resist higher temperatures, like aluminum silicates. Starting in the Bronze age, the people just used whatever clays were at hand. In the iron age though, it probably became clear that some clays didn't work with iron. It also was probably clear that some furnace designs didn't work with iron. So after learning a certain clay wouldn't work, they found one that did. A furnace that will smelt iron will also smelt copper (1085 degrees C) and tin (231.9 degrees C) and the mixture of the two, Bronze (913 degrees C). So once you've got a good furnace that will smelt iron, you're good to go. Curiously, in Neil Burridge's video, they needed to heat the tin ore to 1200 degrees. Since it's the UK, I assume that's Celsius, but I could be wrong! Not sure why it needed to get that hot, but perhaps you could enlighten me! Now the difference between "cast iron" and "steel" is the amount of carbon in it. All of these kinds of forges generally produce iron with lots of carbon in it. It's true that depending on how you do it, you can get steel, that's the outer layer of the Japanese Kera. However, even in Japanese Keras, the inner layer usually has a very high carbon content in the iron, and the material is used as cast iron. When the Japanese smith comes to look at the kera, they get pieces from the middle if they want cast iron, and pieces from the edge if they want tamahagane (steel). As shown in other videos, they test the pieces to make sure they get what they want. It's not that easy to produce low carbon steel in one of these bloomery furnaces as above though, so most of the time, they really only produce high carbon iron, or "cast iron." If you look at the last video, it's clear the bloom of iron they produce is crumbling! I'd be surprised if there's any steel in there, but it's not impossible. It turns out that some of the iron age iron is a combination of "wrought iron" and steel, because clearly some steel can be produced in these primitive foundries. However, at least in a bloomery furnace like the one above, it's a lot easier to produce high carbon iron, hence, the predominance of cast iron. I suppose it depends on your definition of what is "nicely malleable, ductile iron." If it crumbles a couple of times, then becomes workable, is it steel, cast iron, or a mix of the two? I don't think the first iron age smiths knew, but they were happy with it as long as it worked! The technology to smelt iron sand is different than the technology to smelt other ores like hematite as well. It's actually easier to get steel with the Japanese techniques used to smelt iron sand than the ones used in bloomery furnaces for hematite.
-
As far as I know, the working of "cast iron" was the earliest form of iron working. If you throw a piece of iron containing rock in one of the bellows-fired clay ovens they used to smelt copper, it would also smelt at some point and burn white hot. When you work this though, it crumbles as you would expect cast iron to crumble. If you just keep hammering it though, it gets more and more workable until it becomes wrought iron. All of the technological refinements mentioned here are just that, refinements of the basic process so they don't have to sit there hammering it forever!
-
I thought the first video was a fascinating video, and I thank the OP for posting it. I watched it with my 4 year old daughter, and she also thought it was fascinating. She kept asking me: why are they getting burned? I can’t help but feel though that a big part of the difficulties they have is the process itself. One part is the leadership of Kihara Akira, the murage. He provides some direction, but I don’t think his direction is very effective. They produced perfect tamahagane on one side of the furnace, but he says it doesn’t look good initially. They seem afraid to ask him questions. Also, they literally have someone with a PhD in metal extraction from ore, and he just sits there and doesn’t ever say anything. Horio is the best sand adder, so really he should just add all the sand, and the other workers should take care of his other duties, which he doesn’t do as well. Miura is the best manager, so that is what he should be left to do. He’s not bad at adding sand, but not as good as horio. Another part is that they make a lot of mistakes because of exhaustion. This is partly because the furnace is too big, and takes too long to finish the process. As has been mentioned elsewhere, they never get good tamahagane in the middle of the tatara. It only makes sense to make the tatara narrower, which will take less time to complete. Also, it’s clear they’re still working out the process. When this is occurring, it makes sense to run smaller test runs to perfect the process, then only run the big run when everything is optimized. If they run a tatara at 1/4 the size four times, and have everyone do what they’re good at, they’ll get the really good tamahagane every time, and they won’t be so exhausted each time. Apparently this is what was done in the past, they only went to bigger furnaces to try to increase efficiency. They show the students how they do it with a smaller smelter, so clearly it is possible! Other problems with the process is the charcoal management. The charcoal managers are experts, but they are rarely consulted, though the quality and positioning of the charcoal is clearly essential to the process. Really, they should sort all the charcoal by size before the process starts, and be always strategically adding charcoal. Instead, they just get big scoops of it and dump it in, even though the charcoal handlers know that isn’t the best idea. At one point in the back they threw a lot of big pieces of charcoal in, which helped temporarily with a problem, but then that ruined that layer of the tamahagane. It's probably better to strategically add charcoal from the start. There are lots of design optimizations that could be made. For one, they need a better way to manage the slag. Slag viscosity isn’t a mystery, the lower the melting point of the slag constituents, the less viscous the slag will be. One part of this is how the sand is added, if they add too much iron sand near the yujiana, it will increase the melting point of the slag there, causing it to plug. To help prevent this, they can use graphite or ceramic guides to make sure the iron sand only falls where it should. Another part of this is they can add materials with low melting points to help thin out the slag. I think it’s interesting that they only added salt on one side of the tatara, and that’s the side that the slag flowed better out of. The melting point of sodium is 97.79 degrees C. Why don’t they just use more salt? I guess it's not that great to be inhaling a lot of chlorine gas, but there must be something they can add that will help. Also, what some european bloomeries do is to stack the ore and the charcoal in the furnace before. If they design a matrix that holds the sand appropriately, they can integrate some iron sand into the tatara before the process even starts, which will increase efficiency and help to ensure the outcome. Also, their ability to deal with the slag is limited by their strength, the limits of the tools they are using, and the strength of the clay walls. In industrial processes, the machines are designed to automatically manage the slag so humans don’t have to. If they built the furnace walls and designed a machine to automatically drain the slag from them, they will get more consistent results. They could also design better slag clearing tools that don’t take as much strength to use. The yujiana’s are also pretty small. If they use better materials than clay for that portion of the smelter, they can make bigger yujiana holes that will be easier to drain. It’s clear that using clay bricks is a liability in this process, since they are frequently at risk of breaking/leaking/falling over, and it’s hard to make yujiana holes that are big enough. They can design furnace walls with graphite or other ceramics like they do in industrial processes to make that portion of the furnace more reliable. The air supply is also a problem, as if the slag blocks the air entry, it can ruin the process. They should design multiple air holes vertically, and have a system where the air can be shunted higher if an air hole is blocked, even if only temporarily, to help ensure even quality of smelting. For instance, they can use ceramic wool to make the air lines so they are flexible. Also, it seems to me that air flow out of the system will probably make a difference. Most Japanese forges have a fume hood, if they had a fume hood and managed the exhaust of gasses with fans it would probably make the system more efficient. They could also use fans or bellows to keep the air flow in steady as well, which would probably significantly decrease the time it takes to complete the smelting. These components could be reused each time. Let’s not forget that the tatara process was established to increase efficiency of iron production, and that prior to that they used smaller smelters that achieved the same thing. They also did dozens of runs, one after the other, so the crews became skilled quickly. By the time a year rolls around, a lot of the workers have forgotten what they did last year. Better to use the iron sand and charcoal in smaller batches with a more guaranteed result. But let’s say they implemented all the improvements (I’m sure they could think of more!) and greatly increased the yield of good quality steel the furnace makes. Would it still be tamahagane? Tamahagane is worth 1000 times the price of iron smelted in an European bloomery. I think the constituents of the iron sand make a difference (among them the titanium), but I think also part of the value is the mystery and the difficulty of producing it. Someone looking at the more efficiently produced iron would probably say it’s not as good, just because the process was tampered with! I also thought it was fascinating that they tried to teach youngsters about tamahagane with a smaller furnace, but they didn’t want to get dirty or burned. It was a fascinating contrast, because it’s actually reasonable to not want to work yourself to exhaustion and get burned and dirty in the process! However, their sheer grit was admirable. It’s also frustrating to put so much time and effort into a process, without knowing if it’s going to turn out! Most of the crew is older, so who is going to take it over once they retire or die? Clearly it only operates with substantial financial input from the iron refining company, the tamahagane itself doesn’t pay for the process. So doesn’t it make sense to improve efficiency, to increase feasibility? Well, this was my first post and it just might get me banned, but I couldn’t help it! Still, I think it is a fascinating process. I just can’t help but think there’s a better way! I don't think that iron smelted in the factory shown is as good as tamahagane, but there must be some kind of middle ground. Here’s a source I was talking about: https://www.tf.uni-kiel.de/matwis/amat/iss/kap_b/backbone/rb_6_2.html\ The author also posits numerous refinements to the tatara process in the articles, among from I probably picked some up.