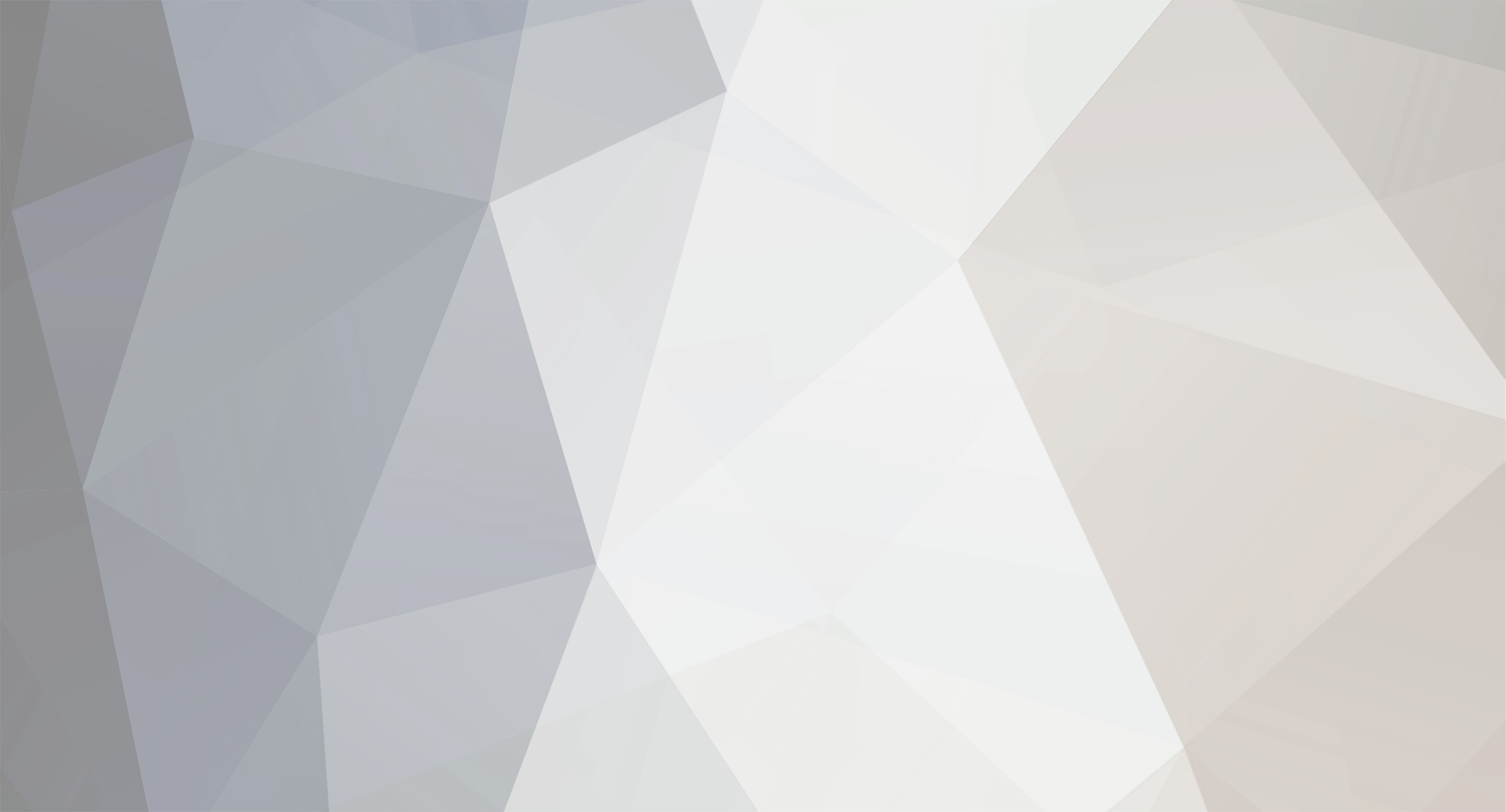
Larason2
Gold Tier-
Posts
245 -
Joined
-
Last visited
Content Type
Profiles
Forums
Events
Store
Downloads
Gallery
Everything posted by Larason2
-
Steve, I think Ford made his observations from the first two photos. The colour in the two Ana is that of pure copper. After a while, you come to recognize certain alloy colours you work a lot with. Shakudo has a fair bit of gold, (37.6% in Ford's recipe), so it's not very economical to make a tsuba out of pure shakudo. Then, only certain other alloys, like pure copper or shibuichi won't interfere with the patination process. Pure copper can also have a range of colours with patination from brown to orange, up to a bright red. So it might have actually also been a conscious choice as an accent colour in the tsuba's ana.
-
The koma nagura from Namikawa Heibei isn't tsushima-do, but I suspect it can work similar. It is quite soft, so it will likely desintegrate a lot like the water of ayr stone, and it is very fine grit like the Tsushima stone and other nagura stones. Tsushima stones are pricey. The cheapest I found for myself in Canada is here: https://www.fendrihan.ca/products/kuro-nagura-Japanese-natural-slurry-stone?currency=CAD&utm_medium=cpc&utm_source=google&utm_campaign=Google Shopping&gad=1&gclid=CjwKCAjw29ymBhAKEiwAHJbJ8qckwnbrB-V18ZHyVrhf8wq_on0FWVu3Xabds0HJJqEUtILfZJv6ixoCZn8QAvD_BwE
-
Damon, looks to me like the second Echizen Kinai piece was lacquered with urushi. That was a common practice. There's nothing about the tsuba that makes me think it was cast.
-
Nagura stones are usually quite a fine grit, something like 5000-8000. The black nagura Ford is talking about would be along those lines. Just google "black nagura" or "kuro nagura." They are only mined underwater in Tsushima. You can probably also get what they call a "koma nagura" stone, that is what I would do, they are fairly economical. These are the second finest stones used to polish a Japanese sword. Namikawa Heibei sells a small one for polishing the bohi of a Japanese sword you can probably cut in 4 for tsuba: https://www.namikawa-ltd.com/product/65 As far as I know, Urushi watanabe.net is the only source for magnolia charcoal to foreigners. They have the 100g and the 500g. Here's the 100g: http://www.urushi-wa...gi?sort=4&word=L0298 I got the 500g, which is enough to last you a lifetime! 500 comes in a fairly big bag with multiple large pieces in it. You have to cut them to a smaller size to use. Both stores are currently on vacation, so you'll have to wait at least a week for your order to be filled! I have ordered from both, and it was a good experience. Jim Kelso has a tutorial online of the Rokusho patina, also called "niage:" https://www.jimkelso...na.html/tutorial.htm Ford also has an excellent and very detailed video he produced on how to go about Rokusho patination, which I would say is about 10x more useful than Jim Kelso's article, but it may only be for his Patreon subscribers. So I'll wait to see if he says it's ok before sharing it. I'll only share one spoiler, and that is it's best to use fresh or frozen daikon radish. Regular radishes will work, but not that great. I found a big daikon locally, and froze most of it for future rokusho experiments! The rokusho you have will probably work. The same material is used as a pigment, called "malachite". Depending on how fine it is ground, it becomes whiter looking. I ordered some "malachite" pigment from an art supplier, since it was much cheaper than rokusho. I haven't tried it yet, but I suspect it will probably also work. Mine looks a bit finer ground than yours.
-
I think there are definitely grades of uchiko, which is just ground up uichigomori do stones. The grit on those stones is very fine, but if you press too hard, you will remove the product of the final finishing, thus losing detail. Also, if it's too cheap it might not be ground fine enough, which could cause a scratch!
-
Interesting, thanks for posting! I also found it interesting that they used primarily the edge of the stone for the komonagura do and uichigomori do polishing steps, and that they use those tiny stone fragments for the final finishing! They talk about the second son and third son, I wonder what happened to the first son? They have quite a nice setup there, a whole room to devote to polishing!
-
I don't think there's a hard and fast rule, but they were probably either threaded through the loop around the ring (sarute) (like most sword tassels), or attached to a pin like the one you show. The Japanese didn't like gluing parts that might have to be replaced, and even after they started having screws, they didn't like using them. With WW2 gunto though, they may hve used a screw to hold together the pin for the tassel. I would guess that for ancient pins through the sarute eyelet, they either used a pressure fit for the pin, or a two part pressure fit like a rivet. There was a lot of variety in tachi fittings though, and many different schools that did them. They also made other fittings for the tachi, including tsubas, and they could be very ornate.
-
Apparently, the tassle on the end was to help prevent dropping it when you lose your grip, the sarute just a ring or eyelet for the tassel. Tassels were and still are very common on Chinese swords, where they serve the same purpose, but on Japanese swords they are less present, because Japanese sword styles tend to grip the handle of the sword more, making it less likely to slip from your grasp.
-
Kinai tsuba were 17th to 19th century, Echizen province of Japan. There's another one with this theme on the Ashmolelan website: http://jameelcentre....0/EA_X_10458-a-L.jpg But I agree it doesn't look typical. But I have no reason to doubt the signature! I quite like it, thanks for posting.
-
Yasurime can be done with a scraper or with a file, it depends on the particular effect you're going for, and which is easier/possible!
-
Haha! Yes, that was just for fun, and I agree the wikipedia article is a fun one. The two animals do look alike though, so I can also understand the confusion.
-
Haha, just to stir the pot, are we sure it's a tanuki and not a mujina? I'm used to tanuki having broader faces, and the mujina are supposedly the ones that inflate their belly and drum them. In some places in Japan, they use the same word for both. https://en.m.wikipedia.org/wiki/Mujina
-
Another related point is that generally, the edges shouldn't be too crisp. For uchikaeshi, they need to be a little crisp, but for most cut outs, you can round the corners quite liberally. For instance, in the top tsuba, while the mimi can be square, you should round the corners on the cut outs of the inside of the tsuba a bit more. This accentuates the texture, and makes it less "stiff" looking. This is also visible on the octopus. The heavily square edge of the cutout looks square, whereas the tentacle would look more natural if you had a gentle curve on all the "smooth" surfaces like the tops of the tentacles. Some of the octopus's limbs look perfectly straight, whereas a real octopus never does that! a gentle curvature makes straight parts look more natural, and liberally curved edges gives a more organic look.
-
No problem! What I mean is that a flat surface, while it looks flat, should never be flat but ever so slightly curved (as Ford would say!). This applies to every "flat" or plain surface, like the side of a uchikaeshi mimi. In the case of the mimi, part of the preparation is filing it so it is slightly round (should not be easily visible, particularly to the uninitiated), say a radius of 1 degree. The corner would then not quite be 90 degree, more like 89 degree, but for all intents and purposes, it still looks square. On the face of a "flat" tsuba, it should have a slight curvature, which you can carve into it, forge into it if the material is compatible, or file it down before you start carving. The part that sits under the seppa can be perfectly flat, but that is an exception. You see Ford do this quite often. He also puts very slight offsets, say the omote of a fuchi 1 mm longer than the ura side and slightly curved, and the blade side of the fuchi slightly longer than the spine side, which are almost invisible, but that help make the piece more human. For this reason, usually Japanese tsuba are not perfectly round, and tend to be taller than they are wide, even if they are meant to look round. They also tend to make the corners of a "circular" tsuba a little bit squarer, not perfectly round. Ford does this starting at the cutting step, but for certain things like the mimi he works primarily with the file, which is also very commonly used by Japanese togishi.
-
Two more thoughts: One is that even if a piece has "sharp edges" in metalworking, they should never actually be sharp. This is also where a file comes in, or judicious use of the scraper. The other is that in the Japanese tradition, even if something is meant to look totally "straight," it should usually have a very gentle curve. Most of your tsubas have this at least on some part of it, but some like the first and the octopus one, seem to have straight edges that are too straight. Giving them a subtle curve makes them more human, and that's more Japanese. I'd recommend you subscribe to Ford Hallam's patreon channel and watch some of his videos. You have good technical skill, but what is missing sometimes is the philosophy or art of the tsuba, which Ford gets into in most of his videos. Especially when you're doing utsushi, it's important to get into the mind of the original creator, and see and do things as if you were them, and spend a lot of time meditating on what it is you're conveying and why you're conveying it, what is the meaning behind it (hard work!). That will take your art to the next level.
-
Your tsuba are very nice! The cutting and carving are quite good, and you've done the patination on them very well. They also adhere to traditional Japanese design quite well. My only comment is that usually yasurime is usually done with a file, and that I consider knowledge of the use of a file essential for good metal working. But you are well on your way, and I think that your post is appropriate for this forum.
-
Ah, fair enough. Still, not a bad polish for a non-professional! Would a professional togishi have worked on this?
-
It is papered. It was submitted to shinsa, and their opinion was it's a historic blade, and referred to a better authority for that. All that paperwork comes with the sword, as it says in the write up.
-
That is amazing! Shows you what a professional polish can do.
-
What about this paper? https://www.nature.com/articles/s41577-019-0221-9#:~:text=It is widely accepted that,to chronic antigen stimulation4. Seems to make biological sense to me.
-
A lot of saya and Japanese armour makers have claimed this has happened to them. It doesn't mean that T cells are not induced, but rather that the T cell mediated response is downregulated with continued exposure over time.
-
Apparently if you keep working through the discomfort and itch, you eventually become immune to it. Doesn't sound like fun though!
-
I'm developing the skills to make koshirae, hopefully eventually to be able to make my own Japanese style knives and swords. Part of this is having a name! I've thought of doing some training in Japan, but my current life situation would make that difficult or impossible, at least in the near future. I studied a bit of Mandarin in school, so I know a bit about Kanji, but not enough to be confident a particular name wouldn't be embarrassing, particularly when we're talking Japanese kanji. So, here's the name I'm thinking about using: 松山雪 My understanding is it means matsuyama yuki, or pine mountain snow. Matsuyama is also the name of a city in Japan, on Shikoku island, apparently named after the mountain it is on. If those of you who know Japanese language and culture could just let me know if it's ok to use as a signature, and doesn't mean something embarrassing, or is a faux pas, because I'm using the name of a city as part of the signature? Thanks!
-
Most people are allergic to poison ivy! The contact reaction you get to poison ivy, you will probably get with urushi. For that reason, it is difficult to work with. The guides I've seen online suggest to use gloves, but not sure if that totally prevents the contact dermatitis. You also need the special moisture controlled box, as commented on. It is also extremely time consuming to polish between steps. So, it's not easy to work with, but it is the original material, and in my opinion, the most beautiful. Definitely not for everyone though. If you just want a black finish, you can just get a black lacquer at your local big box store, and you can even spray it on.
-
To do justice to the piece, you should lacquer it using urushi, and unless you are already very experienced, should probably be done by an expert (but that won't be cheap!). It is typical for urushi to be applied in layers of different colour, each corresponding to different grades. It looks like a lot of it has been worn off, probably through damage. The base coat/coarsest urushi is usually a grey colour, and here it looks like the layers were a light brown, dark brown and then finally black. This corresponds to different grades of urushi as well.