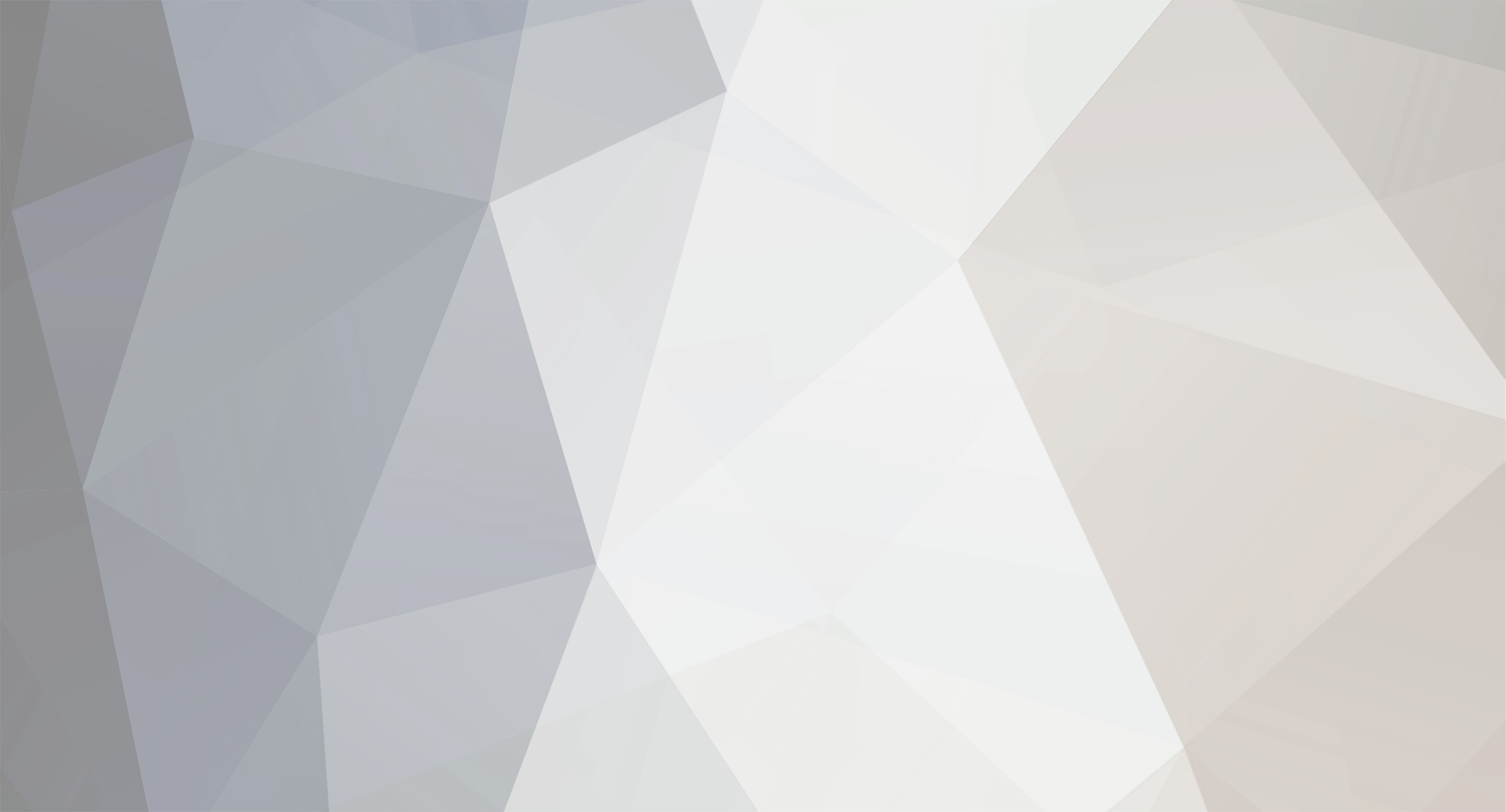
OceanoNox
Members-
Posts
324 -
Joined
-
Last visited
-
Days Won
1
Content Type
Profiles
Forums
Events
Store
Downloads
Gallery
Everything posted by OceanoNox
-
Thank you folks, that's helpful. I had seen some seppa that had seemed to follow the bohi, but I did not know it was supposed to be like that. Most of what I had seen was probably mass produced.
-
Hello all I have been mulling over the possible designs of seppa. I know of the "scales" like design, and the crenelation like design, but I have been wondering if there are sources or collection showing the different types of seppa. Incidentally, I was also wondering if seppa were made to fit a specific koshirae, or if they were made in bulk and adjusted as necessary. So far, I haven't been able to find much about the topic, despite the fact that they are a very important part of the koshirae.
-
Magnificent, Jussi. Thank you very much for you hard work and for uploading the data.
-
Beautiful! Congratulations!
-
Dan, you are being dishonest here, and I am being polite. The very first photo in the "Silver ring in tsubas" (https://www.militaria.co.za/nmb/topic/52786-silver-ring-in-tsubas/#comment-551308) is taken at an angle, and there is nothing in the surface roughness indicating casting, rather it is a look one could easily obtain during forging. My opinion is corroborated with more than 10 years working in research in mechanical and metallurgical engineering, reading actual academic research on the topic of tsuba (as well as period documents, when possible), and trying my hand at the different DOCUMENTED techniques of tsuba making. And if you are looking through my commenting history, you would see the links or references I have posted (I am even the one who posted the research report for the archeological find of cast soft metal tsuba in Nara). If anything, I always try to give a reference to support my opinion. Do it then. Find one of these supposed antique cast iron tsuba, and have the tests made. Or send them to me to do it. I have access to X-ray, electronic microscope with chemical analysis, and micro-hardness (not quite non-invasive, but still considered relatively non-destructive, if you can bear a barely visible indent). Put your money where your mouth is and do the analysis, instead of telling others that they are close-minded and scared, then taking offense at being called out. I am doing it. I had an idea about tsuba research, and my students and I are doing the calculations and experiments to see it through. It's not cutting edge, it's probably not very noteworthy, but we are doing what's necessary to find out if we are right or not.
-
The original picture shows roughness, which is very easily attributed to rough forging, rather than casting. If anything, casting a liquid metal might leave a flatter surface, albeit with maybe a sand-like appearance. But, I may have mentioned this somewhere in the 20 pages here, and I am certainly not the only one: we cannot judge if a tsuba is cast iron from photos alone.
-
Dan, the first photo in the original topic about that tsuba shows that area is flat. Why would a non-flat area be indicative of casting?
-
I agree: In "Japanese aesthetics and culture: A reader" edited by Nancy G. Hume (recommended a long time ago on one forum by the late Ford Hallam), there are indeed clear quotes about the evolution of the wabi aesthetics praising the partially bloomed flower bud, the moon hidden behind clouds, etc. There is quote from the Tsurezuregusa stating "Even when building the imperial palace, they always leave one place unfinished". I don't see how not perfectly filed decorations is any indicator of casting whatsoever (If I showed some of my early sukashi tsuba, some might think I knew how to cast iron...). It might be on purpose, it might be a skill or equipment issue.
-
https://www.comokin.co.jp/shopbrand/004/X/ https://www.tools-shop.net/view/category/g-engaver14 These are the usually recommended sites for tools. I have no idea if they ship abroad. Like Manuel said, most make their own. I have made some tagane with old broken files, after annealing them (it is very time consuming, but rewarding) and a few kisage as well. You can buy tool steel (if you're in France, I don't know the equivalent, but here is the wiki: https://fr.wikipedia.org/wiki/Acier_à_outils).
-
Transition from koto to shinto periods
OceanoNox replied to Mikaveli's topic in General Nihonto Related Discussion
FYI, from two sets of experiments done in the early 2000s with bladesmiths (published by Prof. Takuo Suzuki), there is little evidence that the "impurity" content (I mean atoms that are not interstitials, like carbon) actually changes with folding. Only the carbon content and the amount/shape/distribution/size of inclusions changes with the folding and forging process. About the effect of composition, it has a clear effect on oxidation, but I am not aware that it changes the colour of polished steel. Forging indeed will give you smaller grains, but then again, how the smith heats the blade prior to quenching will also change this grain size. There was a very nice study in Prof. Morito's team where they managed to show how different the grain size prior to quenching was with different smiths. Also, I thought a lot of the final aspect of the blade depended on the polisher. But here, I have virtually no knowledge. EDIT: All that to say that I think the carbon content, the smith, and the polisher have a larger effect on the final aspect of the blade than the other elements present in minute concentrations. -
Transition from koto to shinto periods
OceanoNox replied to Mikaveli's topic in General Nihonto Related Discussion
Can the slight variations in chemical composition really be seen on the blade? There might be slightly faster or slower grain growth due the elements in the steel, but I thought the forging and heat treating process of each smith would have a stronger effect on the final appearance of the sword. By the way, Prof. Ohmura has a page on this various structures of the swords across time/styles: http://ohmura-study.net/008.html -
That's the issue with this thread, as raised earlier (and I know I am contributing to the problem, but at this point, it's too late): all the interesting information is hard to find. The reference to that paper (cast sword fitting in brass) has been given at some earlier point. Just like the mention of cast iron items, like chagama, and the process of doing it (cast the cast iron, then decarburize, finish the surface, then patinate it). Cast iron tsuba are currently made by iai equipment maker Nosyudo, but I am not familiar with their process (I suspect it's similar to the one above). Reference on non-ferrous cast tsuba in Nara: 刀装具鋳型の三次元分析からみた近世鋳造技術の研究 (2018 年度科学研究費(奨励研究)研究成果報告書, 研究課題番号:18H00015)
-
New Shinken Purchase! Gendaito - Akamatsu Taro Kaneyuki
OceanoNox replied to Charliebrown's topic in Nihonto
Nice blade! I have one from that forge (in Kumamoto, right?). They are really exceptionally well balanced for iai. Congratulations, enjoy it! -
On Instagram, this artisan makes beautiful bags (based in Japan, but may take orders?): https://www.instagram.com/okatanabukuro_waka/
-
From my understanding, kacchushi tsuba are usually thin, round, and large, with a worked mimi (like uchikaeshi mimi) that is thicker than the ji. Sukashi is usually a bit more elaborate than what is seen on the so-called tosho tsuba. I cannot judge the thickness here, but from the nakago ana, it is a bit small.
-
Mumei Kanayama tsuba that point to a specific tsubako
OceanoNox replied to Iaido dude's topic in Tosogu
That sounds interesting! Can you share what you are doing? -
Thank you for your hard work and for the link!
-
In iaido, shinken is recommended eventually. It may implicit, but for 5th dan onward, shinken is practically mandatory for testing and taikai. If you go to a dojo with high ranking practitioners, there are no mogito, only shinken being swung around. 900g is fine for a iai shinken. If it has a bohi, like most swords for iaido to avoid tennis elbow and such repetitive joint injury, it is not recommended for cutting, especially if you are a beginner, since it is a bit easier to bend. Weight distribution rather than total weight is more important for iai, but you need to swing the sword (single-handed) to check if the sword fits you. The sori and kissaki shape are also very important (I know a person with a sori almost like a tachi, but he is an exception). N.B.: For comparison, my own shinken for iai (I do ZNKR iai and muso shinden ryu) is 79.6 cm long (sori is 2.0 cm) and about 970g. The blade tapers towards the tip, and it feels like a feather compared to my mogito.
-
Do you remember where you read/heard that? It's very interesting to me. In my comment above, Isawa talks about failure (and I think there is another who talks either about mekugi failure or failure at the habaki). My student did a calculation, and the kachushi tsuba with a thick mimi "keeps" the shockwave bouncing around in the tsuba, for instance. I wonder who much it is mitigated with everything else. PS: It might be Yaso who published a paper about impacting a Japanese sword. They identified the nodes: at the monouchi and at the mekugi, i.e. where the vibrations are smallest. When doing it on a naked blade, there was some vibration at the nodes, but with a full koshirae, the vibration was basically 0 at these nodes.
-
People don't aim typically for the sword either, but if you block and control your opponent's weapon, a guard of some sort helps with that purpose. With how it's wielded, a tsuba also makes a lot of sense on a nagamaki than a naginata. @O koumori here are some info I got from earlier sources about tsuba: "鍔は只拳の楯と聞物を太くも太くもなきは非がごと" in a Hayashizaki shin muso ryu scroll dated from 1601 (if memory serves). This one calls a tsuba a "shield for the fist(s). Tsukahara Bokuden wrote: 鍔はたたふときにしくはなきものを細きを好む人そ拙き 皆人のしらてや恥をかきぬらん鍔のつめある習ありとは 鍔はたた切ぬき有を好むへし厚き無紋を深く嫌へり あら鍔はいかに厚くと切れぬへしたとへ薄きも古き好めり It does not directly refer to tsuba as hand protection, but states what should be preferred in terms of design. In 1719, someone called Isawa (井澤蟠龍子, in 武士道叢書) wrote: "鍔は無地の厚きを用へし 大サ三寸四五分短刀(わきざし)の鍔三寸ほどにすべし 見るところのよろしからんを思ひてすかしあるうすき鍔を用べからず打合とき切破ことあり" which states a preferred design for a tsuba to resist blows (along with the sword itself). I couldn't get the direct citation, but it's cited by both Nagaoka (1942) and Sasano (1975): in the essay 鈴林類纂 (Edo period), tsuba are recommended to be essentially like kachushi tsuba (thicker mimi than seppadai, have some, but not too big, sukashi). The shape would prevent damage to the mekugi when hit, and the small sukashi would prevent blades from going in them or catching them. Now, the issue is why all those are not in accordance with one another about design. At any rate, the first is clear, the others are less direct but imply that tsuba are hand protection. The funny thing to me, is that all the works that say tsuba are for slip prevention (like in the Art of the Samurai: Japanese Arms and Armors 1156-1868 catalogue of the MET), I have not seen any period source being cited.
-
Unfortunately, I have even seen the MET catalogue on samurai, written by the Tokyo National Museum curators, specifically say it, adding that it was not for protection from blows. Sasano as well talked about the tsuba being to prevent slipping, because thrusts are the best attacks against someone in armour. Nevermind that we have tsuba on tachi, whose curvature makes the idea of a thrust dubious. Just like @Jacques wrote, koryu teach to use the tsuba to protect your hand or catch an enemy's weapon. Shinkage ryu does too. It is clear from koryu documents that tsuba were thought as a protection from blows for the hand.
-
Some of the results come from a study made by Nippon Steel (新日本製鐵第一研究所) using CMA (Computer-aided Micro Analyzer or Comprehensive Multi Analyzer). It seems to be like EPMA but faster and with a larger analysis area. Unfortunately, the paper does not give the details of the research report...
-
I have to admit I haven't read much outside of academic work on Japanese swords. I am trying to remedy that by reading stuff written by Alan Williams, and get to other stuff, the goal being to understand the similarities and differences in methods and goals when making swords (I am still not sure why the Japanese apparently aimed for such high hardness). That being said, so far, the body of academic work on Japanese swords, in particular material science and mechanical properties, is quite consistent, whether it's about old swords or modern ones.